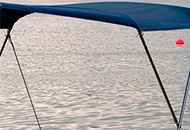
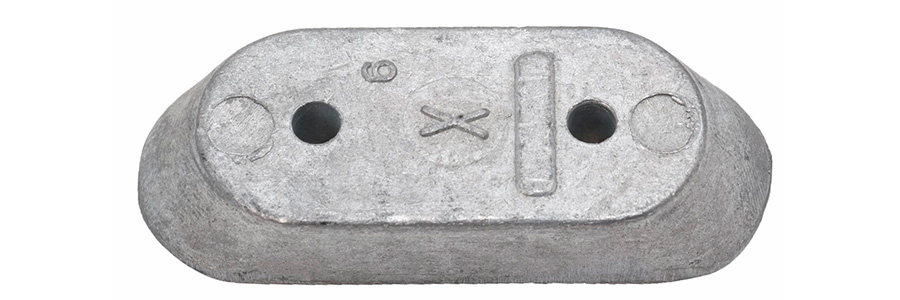
Marine Anodes: Guardians Against Galvanic Corrosion
Marine anodes, often referred to as sacrificial anodes, serve a critical function in the preservation of a boat's underwater metal components. These components include the hull, propeller, shafts, and rudders, which are susceptible to a destructive process known as galvanic corrosion. Galvanic corrosion occurs when two dissimilar metals are immersed in an electrolyte (such as saltwater or freshwater) and electrically connected, causing one metal (the less noble, such as aluminum or zinc) to corrode faster than the other (more noble, like stainless steel).
The purpose of marine anodes lies in their sacrificial nature. They are made from materials that are more electrochemically active than the metals used in the construction of the boat's underwater parts. This means that the anodes will corrode first, thereby offering protection to the more valuable metal components of the boat. The principle behind this protection is the anode's ability to draw the corrosive process towards itself and away from crucial boat parts, effectively sacrificing itself for the greater good of the vessel's longevity and safety.
Replacing marine anodes at the correct intervals is crucial. It is generally recommended to inspect anodes regularly and replace them once they have eroded to about half of their original size, which typically occurs on an annual basis. However, the rate at which an anode corrodes can vary greatly depending on several factors, including the salinity of the water (which affects electrical conductivity), the temperature of the water, the boat's usage patterns, and the quality of the anode material itself. For instance, high-quality boat zincs with a high zinc content are known for providing maximum protection over a longer period compared to lower-quality alternatives.
The consequences of neglecting the replacement of anodes can be severe. Without adequate protection, the boat's underwater metal parts can rapidly deteriorate due to galvanic corrosion, potentially leading to significant damage and costly repairs. Therefore, understanding the role of marine anodes and ensuring they are properly maintained is a fundamental aspect of responsible boat ownership and care.
In addition to their crucial role in preventing galvanic corrosion, marine anodes are designed to address specific conditions depending on the water type and boat usage. For boats operating in both saltwater and freshwater, using aluminum alloy anodes is advisable as they offer protection in varied environments, unlike zinc anodes which are ideal for saltwater but not as effective in freshwater. Boat owners should ensure that their outboard motors, trim tabs, stern drives, and lower units are equipped with the right type of anode to protect against electrolytic corrosion that occurs when stray electrical currents are present. It's essential to keep an eye on internal anodes within boat engines as well, as these are critical for protecting the metal parts like the stainless steel shafts from corroding. Regularly checking and replacing anodes before they deplete to less than half of their original size will help maintain the integrity of the boat’s metal components, ultimately safeguarding the vessel from premature wear and ensuring its longevity.
In essence, marine anodes play a vital role in the preservation and operational safety of a boat. By sacrificing themselves, these anodes protect valuable underwater components from the ravages of galvanic corrosion, thereby extending the life of the boat and helping to ensure a safe and enjoyable boating experience.
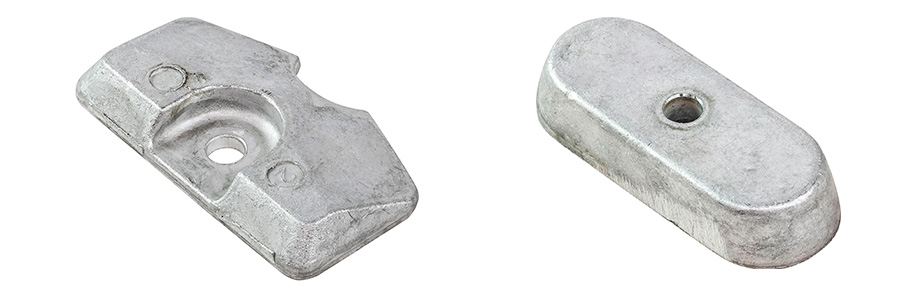
Understanding Marine Anodes: Aluminum, Magnesium, and Zinc
Marine anodes are classified based on the metal they are made from, with each type having specific applications and environments where they perform best. The primary metals used for marine anodes are aluminum, magnesium, and zinc. Understanding the differences between these types of anodes is crucial for selecting the right one for your boat, depending on the water conditions it will be operating in.
Aluminum Anodes
Aluminum anodes are versatile and efficient, making them suitable for use in both saltwater and brackish water environments. Their primary advantage lies in their higher electrical capacity, which allows them to be smaller and lighter than zinc anodes while providing the same level of protection. This makes aluminum anodes an excellent choice for boaters looking for effective corrosion protection without adding significant weight to their vessel. Additionally, aluminum anodes are more environmentally friendly compared to traditional zinc anodes, as they do not contain toxic elements.
Magnesium Anodes
Magnesium anodes are specifically designed for fresh water use. They have a lower open circuit potential compared to zinc and aluminum, making them the most active of the three anode types. This high activity level allows magnesium anodes to provide excellent protection in freshwater environments, where the electrical conductivity is lower than in saltwater. However, due to their high reactivity, magnesium anodes are not suitable for use in saltwater as they would corrode too quickly, offering little to no long-term protection.
Zinc Anodes
Zinc anodes have long been the standard option among Boat Anodes For Saltwater applications.. They are known for their durability and effectiveness in providing protection against galvanic corrosion in marine environments. Zinc anodes are denser and have a higher structural composition, which gives them increased impact strength in some applications. However, environmental concerns regarding zinc's toxicity have led to a greater emphasis on aluminum anodes in recent years, especially in regions with strict environmental regulations.
Choosing the Right Anodes on a Boat
The choice of anode material largely depends on the type of water your boat will be operating in. For saltwater and brackish water, aluminum anodes are generally recommended due to their effectiveness, lighter weight, and environmental benefits. In fresh water, magnesium anodes offer superior protection due to their high activity level. It's essential to match the anode material to the specific conditions to ensure optimal protection against corrosion.
Furthermore, anodes are designed for different parts of the boat, such as the hull, propeller, rudder, and shaft, to provide targeted protection. Proper selection and placement of marine anodes are critical for safeguarding your boat's underwater metal parts from galvanic corrosion, ensuring longevity and performance.
In summary, understanding the types of marine anodes and their respective applications is key to maintaining the integrity of your boat's underwater components. By selecting the appropriate anode material based on the water conditions you'll be navigating, you can significantly reduce the risk of galvanic corrosion and protect your investment.
Understanding Boat Anodes: Protection Against Galvanic Corrosion
Boat anodes, often termed sacrificial anodes, are a crucial component in protecting a boat from the damaging effects of galvanic corrosion. Galvanic corrosion is a process that occurs when two dissimilar metals are immersed in an electrolyte, such as seawater, and electrically connected, causing one of the metals to corrode. To combat this, boat anodes are introduced into the system, designed to corrode instead of more valuable components like propellers, shafts, and outboards.
Understanding Galvanic Corrosion
Galvanic corrosion involves the transfer of electrons between different types of metal in the presence of an electrolyte. This process can quickly degrade underwater boat parts, leading to costly repairs if left unchecked. Anodes are made from metals that are more "active" in the galvanic series than the metals used for important boat components. This means they corrode first, effectively sacrificing themselves to protect other parts of the boat.
How Hull Anodes Work
When installed on a boat, anodes become the least noble metal within the vessel's electrical circuit. This quality ensures that they will corrode or dissolve first before any other metal component. By doing so, anodes prevent crucial parts of the boat, such as the engine or the hull, from galvanic corrosion. The choice of anode material—aluminium, magnesium, or zinc—is dependent on the water environment the boat is predominantly used in, as each material has different properties and effectiveness in various types of water.
Volvo Active Anode System
Some modern boats employ centralized active anode systems that connect all metal components to a large anode, often placed on the transom. This system ensures comprehensive protection by evenly distributing the protective effects of the anode across all connected metals, minimizing corrosion risks.
Material Considerations
- Zinc Anodes: Traditionally used in saltwater, zinc anodes are effective but can become inactive in less saline conditions by forming a passive oxide layer. They're also subject to environmental concerns due to zinc's toxicity.
- Aluminium Anodes: Offering protection in both saltwater and brackish environments, aluminum anodes are lighter and often more efficient than zinc, providing longer-lasting protection without environmental drawbacks.
- Magnesium Anodes: Ideal for freshwater use, magnesium anodes have a high activity level that suits the low conductivity of fresh water but corrode too quickly in saltwater.
Installation and Maintenance
Proper installation and regular maintenance of boat anodes are vital. Anodes should have direct contact with the water and the metals they are intended to protect. They should never be painted, as coatings can render them ineffective. Monitoring anodes for significant wear and replacing them when they are about halfway eroded, typically annually, ensures continuous protection against corrosion.
To ensure comprehensive protection of your boat's underwater metal components, it is essential to understand the role and function of different types of anodes based on the boat's operating environment. Zinc anodes, suitable for saltwater and brackish conditions, are designed to prevent corrosion of vital parts like the propeller and the hull when they are in electrical contact with less noble metals. Magnesium anodes are the preferred choice in freshwater due to their high activity level, which combats the lower conductivity of such environments effectively. However, these should not be used in saltwater as their high rate of corrosion could lead to frequent replacements and higher costs.
For boats operating in varied water types, selecting the correct anode—whether zinc in brackish or salt water, aluminum for both saltwater and brackish conditions, or magnesium for freshwater—is crucial for maintaining the integrity of the boat’s engine, motor, and outboard systems. Regular checks are necessary to ensure anodes are functioning properly and are not coated with bottom paint, which can insulate them and render them ineffective. Replacing anodes when they have eroded to about half of their original size is critical to continue protecting your boat from the damaging effects of galvanic corrosion, thus maintaining your vessel's performance and structural integrity over time.
Boat anodes are a simple yet essential defense against the costly and destructive forces of galvanic corrosion. By understanding how they work and selecting the right type for your boating environment, you can ensure the longevity and performance of your boat's underwater metal components. Regular checks and timely replacement of anodes can save boat owners from expensive repairs and maintain the structural integrity of their vessels over time.
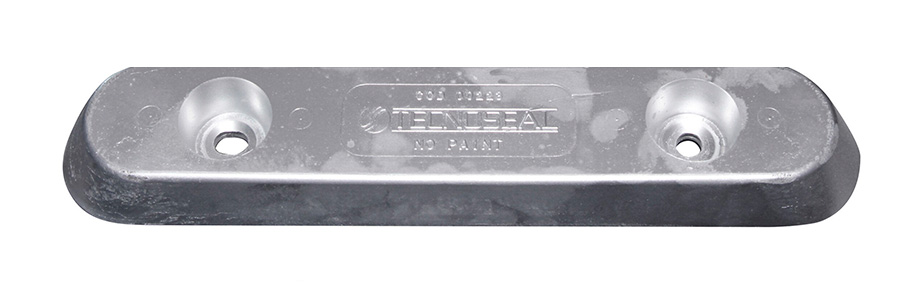
Key Considerations for Anode Selection
Selecting the right anodes for your boat is crucial in ensuring optimal protection against galvanic corrosion. It's not merely about picking any sacrificial anode; rather, it's about making an informed choice based on several key factors. Understanding these considerations will help you protect your vessel's underwater metal components effectively.
1. Type of Water
The primary consideration in anode selection is the type of water in which your boat operates. Each water type—fresh, salt, or brackish—has different electrical properties that influence the rate at which anodes corrode.
- Saltwater: requires anodes with a robust structure and slower corrosion rate, making zinc and aluminum the preferred choices.
- Freshwater: demands more reactive anodes due to its lower electrical conductivity, with magnesium being the ideal option.
- Brackish water: has variable salinity, thus aluminum anodes are often recommended for their versatility and efficiency across different conditions.
2. Boat Usage
How frequently you use your boat and the conditions under which it operates can affect anode wear. Boats that are used more often or are docked in marinas with various electrical currents may need anodes that offer more robust protection or require more frequent replacements.
3. Compatibility with Boat Materials
Ensure the anodes you select are compatible with your boat's construction materials. Anodes should be matched with the metals they are protecting to prevent any adverse reactions or accelerated corrosion of the protected metals themselves.
4. Environmental Concerns
Zinc anodes contain small amounts of cadmium, a toxic heavy metal. With environmental regulations becoming stricter, aluminum anodes, which are less harmful to marine ecosystems, are becoming a popular alternative.
5. Maintenance and Replacement Costs
Consider the longevity and cost of replacement for the anodes. While magnesium anodes offer the best protection in freshwater, they also wear out more quickly than zinc or aluminum, potentially leading to higher maintenance costs over time.
6. Physical Space and Placement
The size and shape of anodes should fit the specific areas of your boat that require protection, such as the hull, propeller, and rudder. Anodes come in various sizes and configurations, so selecting the right one ensures comprehensive coverage and protection.
7. Local Regulations and Recommendations
Some marinas or local waterways may have specific regulations or recommendations for anode materials based on environmental considerations or known water conditions. It's advisable to check these guidelines to ensure compliance and optimal protection.
In addition to these guidelines, specific attention must be given to the anodes that are directly connected to the boat's propulsion system, including boat engine anodes, motor anodes, and outboard anodes. These are critical because they are specifically designed to protect the vital metallic components of the engine from electrolysis, which can be severely damaging. Motor anodes and outboard anodes, often made from zinc or magnesium depending on the type of water, are sacrificial in nature; they degrade instead of the more expensive engine parts.
It is crucial to inspect these anodes at least annually to ensure they are not only performing their function but are also in good condition, showing no signs of being coated or isolated from electrical contact, which can impair their effectiveness. The two metals involved, typically a noble metal like stainless steel and a less noble metal such as zinc or magnesium, need to be in bare and bright contact to ensure proper protection through a galvanic connection. Replacing these anodes when they have worn down to half of their original size or more frequently if signs of corrosion are evident, ensures continuous protection of your boat's engine and other critical underwater metal parts, thus maintaining the integrity and performance of your vessel in any boating environment.
By taking into account these key considerations, boat owners can make informed decisions when selecting anodes, ensuring their vessels are protected against corrosion without incurring unnecessary costs or harming the environment. Regular inspections and prompt replacements of anodes are integral to maintaining this protection, allowing for worry-free enjoyment of your boating adventures.